Karbit OKE Carbide Inserts in Pune. Suppliers & Exporters of Karbit OKE Carbide Inserts in Pune Maharashtra
At Sadguru Enterprises, we are karbit OKE carbide inserts suppliers, dealers in Pune, Maharashtra. We are committed to providing our clients with the best Karbit OKE Inserts available.Our Inserts that are made with the highest quality materials, ensuring that they are long-lasting and durable. We have a wide range of Inserts in different sizes, shapes, and styles to suit your needs and offer competitive prices on all our products, ensuring that you get the best value for your money.
Our experienced staff is always available to provide you with expert advice and guidance, ensuring that you make the right choice for your business. We strive to provide our clients with the best customer service, ensuring that all your queries and concerns are addressed in a timely manner.
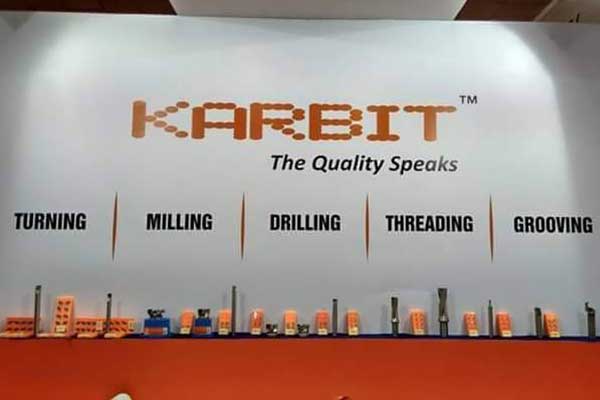
Carbide Inserts Tools
-
Seat – A piece of hard metal that is the same size as the insert it supports. It is usually placed between the insert and the bottom of the package where the carbide insert fits in the tool holder.
-
Holder - This component supports the carbide insert and maintains strength and stiffness to minimize deflection and potential vibration during operation.
-
Boring Bar – Refers to a cylindrical bur for internal machining, specifically for drilling precise holes in workpieces. This can be found in a variety of materials such as steel, solid carbide, and hardened steel.
-
Drill – This is a cylindrical shank with a conical cutting tip with one or more helical flutes designed to eject chips from the workpiece.
How Karbit OKE Carbide Inserts are manufactured?
Carbide inserts are manufactured in different geometries to suit each application. The manufacturing process is therefore very intensive to ensure that precision and dimensions are properly achieved. Here are the steps to create these cutting tools: -
-
Container
These powders are packed in barrels of approximately 80 kg and taken to presses to produce the inserts. At this stage the insert is very fragile and breaks easily. -
Insert punching machine and punching insert
Pressed inserts must be hardened by heating in a sintering furnace. -
Sintering furnace
after the quality check is completed; the top and bottom of the insert are ground to the required thickness. Carbide is very hard and must be polished with an industrial diamond. -
Full cycle grinding
After reaching the required thickness, it needs to be further sanded to get the exact shape and size. A 6-axis abrasive disc is used to meet the tightest tolerance requirements. -
Passivation Workshop
After grinding, the inserts are cleaned, passivated, and coated. Gloves should be worn when handling the inserts at this stage to avoid grease and dust. Completion of the coating means the blade manufacturing process is completed.